What is Flow?
What is the first thing that comes to mind when thinking about enhancing a software application? Features and functionality? Performance? Look and feel? Customer needs? There is no wrong answer to this question; however, one answer incorporates all of these ideas: Flow. It’s perhaps a somewhat unconventional take, but I don’t like to think of software applications in terms of epics and features but rather as simple processes: data migrating from one place to another to serve a customer’s needs. In a word, flow. It can be challenging to think about software in terms of flow, but if we start at the customer, define what is valuable to them and work backward, mapping the steps that deliver that value, data flow and the process often come into focus above individual functionality.
Value Stream Mapping Helps Us Visualize Flow
Considering the complexity of most modern software architecture, it makes sense to abstract ourselves from the individual implementation details (Epics and Features) and instead think about delivery from the perspective of the customer’s needs and how the application delivers necessary value for them. In other words, how well does information flow through our application and does it serve our customer’s needs? With this concept in mind, we can steal some tools, like Value Stream Mapping (VSM), from the lean manufacturing world to better visualize and improve the flow of “Information Inventory” in our applications to better serve our customers.
The Value Stream Map is an excellent tool for capturing critical points in a given process, visualizing material and information flows, and, most importantly, identifying waste in the system. Even without the physical product changes of manufacturing, a VSM can still help us highlight the flow of information throughout an application capturing things like decision points, feedback loops, quality checks, and reviews. Each documented point in the process can be assessed for its value toward the product, allowing us to find and address waste. Using the VSM as a visual guide, we can apply some actionable metrics to each and identify the biggest bang for our buck improvements, informing what work should come next.
Using the VSM and Flow to Improve Organizational Learning
One immediate benefit to using a visual tool like Value Stream Mapping is how quickly it helps identify how superfluous and repetitive many processes are. These processes often don’t feel as repetitive as they are and a VSM activity can help highlight this waste in a service. Visualizing and assessing each step in the process makes unnecessary and redundant tasks, wait times, engineering changes, rework and time to resolve defects immediately apparent and thus addressable as part of a more significant improvement effort.
In the case of information flows, the most common form of waste is waiting for action. We see the most benefits of flow from tightly coupling related processes together. Different roles use software in different ways and on different timelines, many of which do not coordinate with one another. This lack of coordination creates a sort of “information inventory” we must manage. As with physical inventory, it is not inventory volume that is the most important, but rather the way the build-up of that inventory creates delays in the process. This concept of information build-up causing delays highlights the importance of a tool like a VSM. The VSM quickly brings problems to the surface, not allowing them to hide in a build-up of information inventory. The faster problems surface, the quicker teams can engage in problem-solving activities, thus fixing issues faster and improving your overall organizational learning.
A better culture around organizational learning will also lead to an improved viewpoint on how your organization delivers value to its customers. Most agile organizations are interested in working quickly, adapting when necessary, and delivering features and functionality as soon as possible. These are all good things! However, this mindset often leads teams to lose the forest for the trees and become too focused on the minutiae leading to a suboptimal output for the customer. By keeping flow in mind and utilizing a big-picture tool like a Value Stream Map, teams can avoid this pitfall and improve organizational culture along the way.
Reference: Liker, Jeffrey K. “Using the Toyota Way to Transform Technical and Service Organizations.” The Toyota Way: 14 Management Principles from the World’s Greatest Manufacturer, McGraw-Hill, New York, NY, 2004, pp. 271–288.
About the Author:
John Moore is a Principal Business Analyst and the BA Practice Lead at Sparq. He specializes in business process design and optimization, which he uses to support his clients in successfully designing and executing complex software development projects. At home, he’s a father to an incredible little girl, a guitar player, a hobby homebrewer and a board game enthusiast.
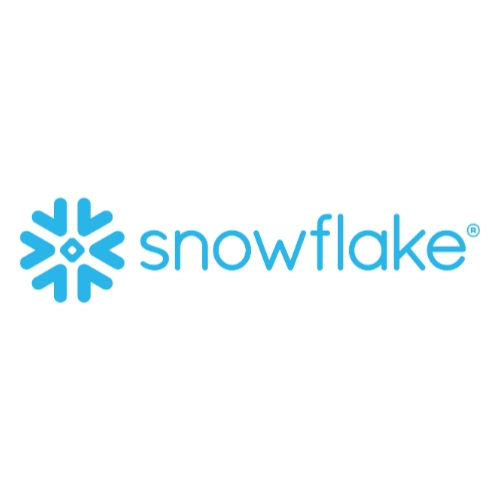
Snowflake Summit 2025 Announcements
Snowflake Summit 2025’s latest announcements made it clear: the path to genuine AI-driven impact hinges on frictionless access to data, the ability to act on it with clarity, and absolute confidence in its protection. Learn more about how they're making that happen for customers in this article.
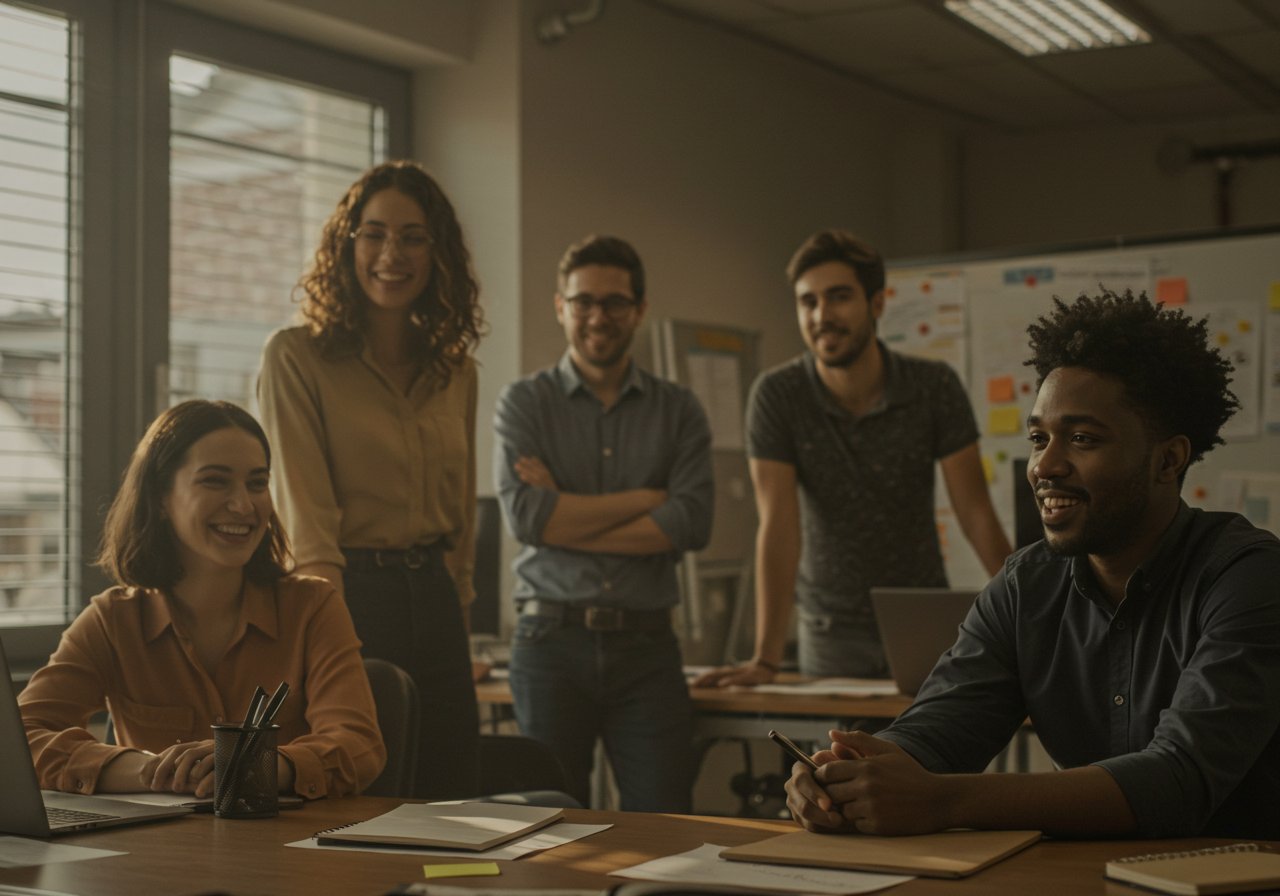
How ChatPRD Helps Build Better Stories (and a Stronger Team)
When user stories are vague, it slows down delivery, trust, and momentum. This article by Senior Product Strategy Consultant Traci Metzger shows how she used a lightweight, AI-guided system (ChatPRD) to write clearer, developer-ready requirements that actually accelerated execution.
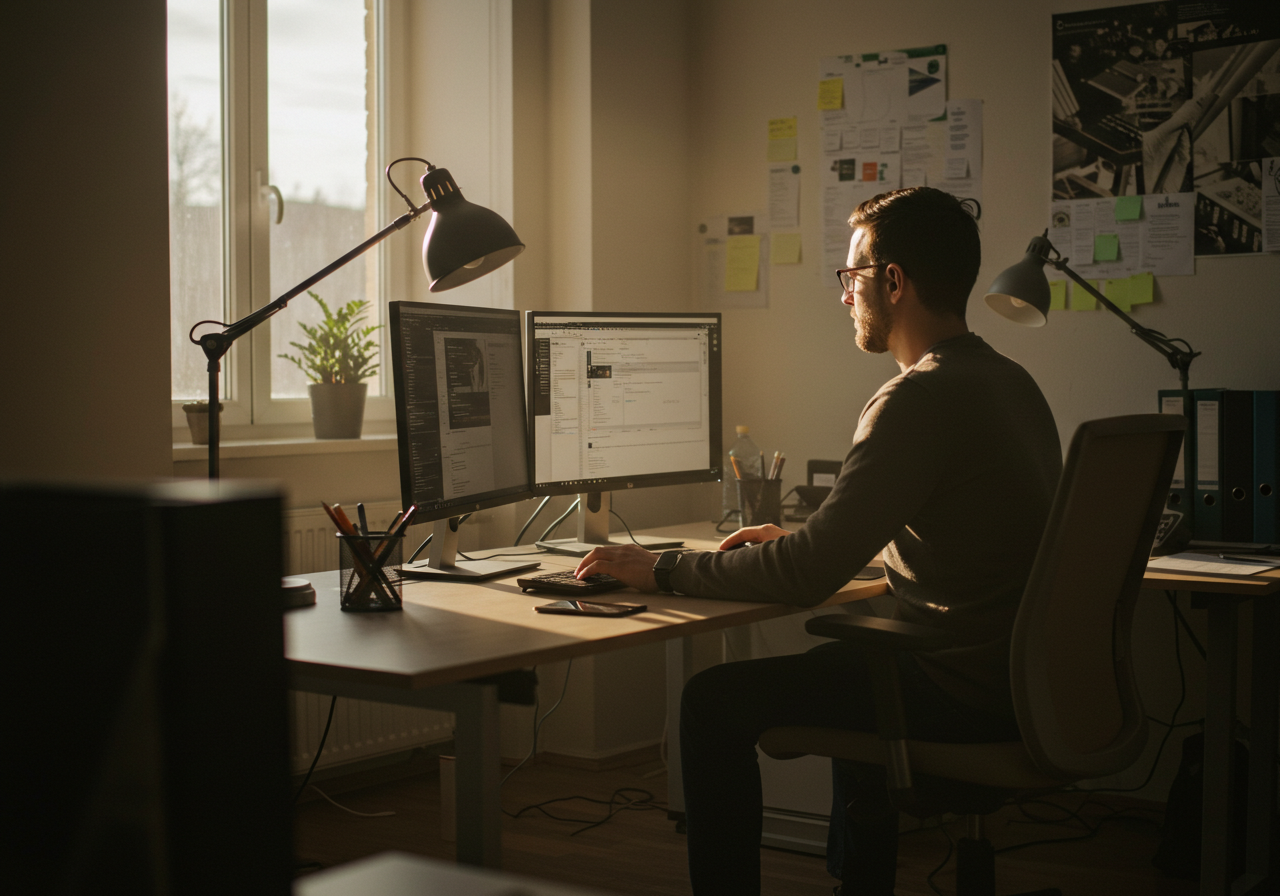
QA in the Age of AI: The Rise of AI-Powered Quality Intelligence
As organizations push code to production faster, respond rapidly to new customer needs and build adaptive systems, the expectations on quality have changed. It's no longer enough to simply catch bugs at the end of the cycle. We’re entering an era where quality engineering must evolve into quality intelligence and organizations adopting quality intelligence practices are reporting measurable gains across key delivery metrics. Learn more in this article by Principal Engineer Jarius Hayes.
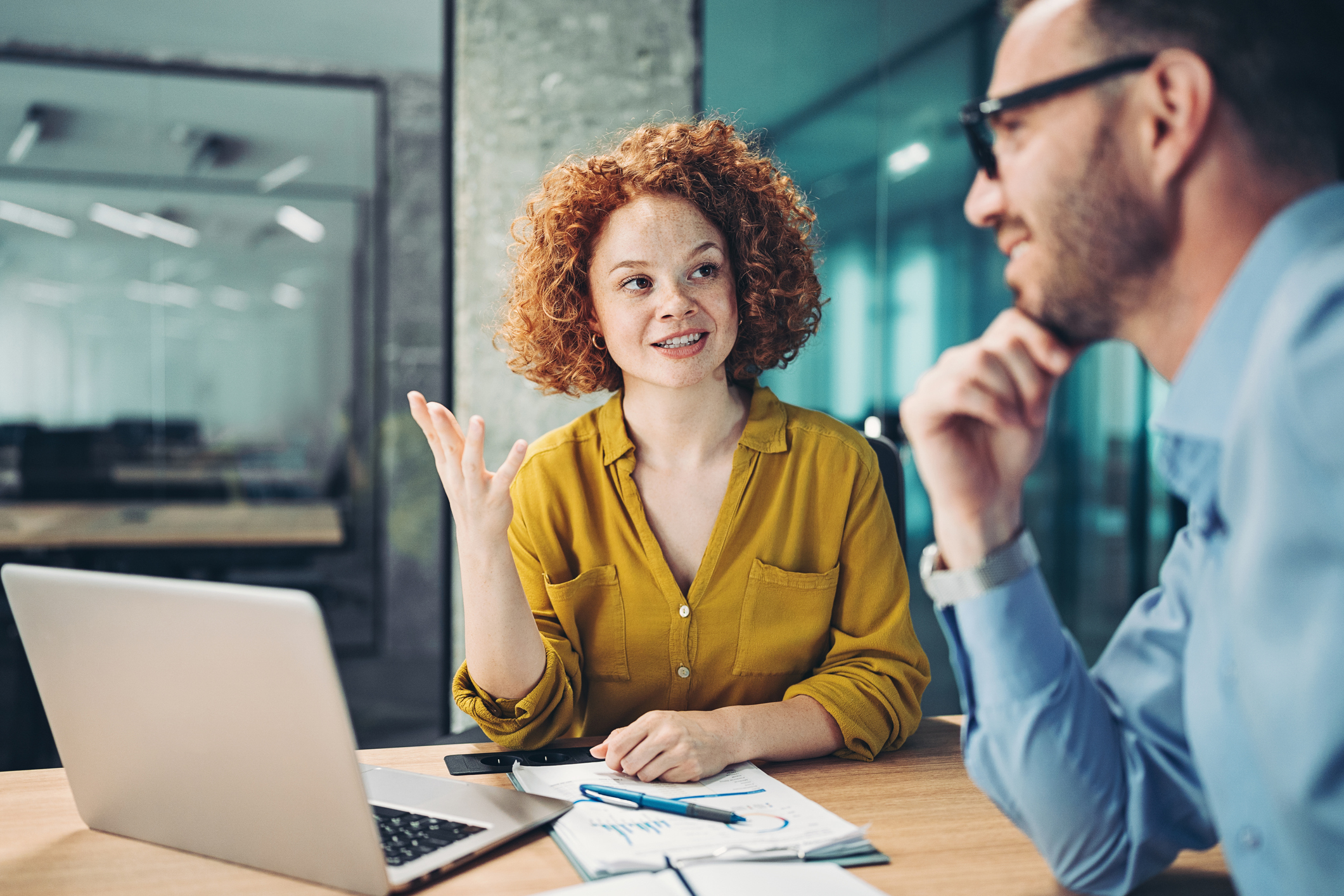
Operational Efficiency in the AI Era: What Matters and What Works
Ever wonder how leading teams are cutting costs without cutting corners? Hint: it starts with AI. In this article by Principal Delivery Manager Kabir Chugh, learn how AI is powering smarter ops, faster deployments, and measurable savings across industries.